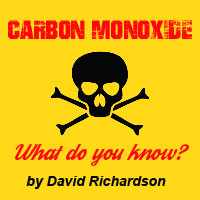
News
Carbon Monoxide: Leaking Gas Valves
By David Richardson
With the floods affecting central Kentucky right now, I thought it would be a good idea to revisit what happened here over 20 years ago. During that event, some HVAC technicians cleaned out water-logged gas valves as they tried to get furnaces running again. I’m sure many of you are shaking your heads since you know those valves could fail in the open position, spewing gas into the equipment and building.
While not all the leaking gas valves you encounter will be this obvious, the potential always exists for them to leak, even without being submerged. Let’s look at a common cause of failed valves and how you can use carbon monoxide (CO) as a diagnostic tool to troubleshoot them.
Gas Valve Leaks
In the early 1990s, the HVAC Industry saw a drastic increase in the number of gas valves being replaced in induced draft furnaces because of supposed leaks. After returning the valves to manufacturers, they discovered no leakage during laboratory testing. Further investigation found that electronic gas detectors were used to condemn those valves. While the test sounds valid, it measured residual fuel in the equipment instead of gas valve leakage.
To educate the industry and prevent the replacement of perfectly good valves, manufacturer’s published a technical paper about how to address the issue. The paper also revealed gas valves can leak a small percentage of fuel according to ANSI standards — approximately 235 cc/hr (cubic centimeters per hour), as measured with a bubble meter.
A Common Cause
While the article focused on misdiagnosed valves, other issues can cause them to fail and leak unacceptable amounts of fuel. The absence of a sediment trap or drip leg is one of the most common issues.
When a gas line doesn’t have a sediment trap, there is no place for residual debris in the gas line to settle. The trap provides a space for materials like cutting oil, shavings, sediment, and Teflon tape scrap to accumulate. If there is no place in the gas line for debris to collect, it can become trapped in the valve’s seats and cause them to warp or stick open.
This presents a potentially dangerous scenario where a fire or explosion could occur. Let’s be clear, this is an installation problem, not a gas valve problem. Of all the leaking gas valves I have found, they all had one common factor – no sediment trap.
Troubleshooting with CO
Most service technicians I know don’t have a bubble meter on their service vans. Without one, how are you supposed to determine if a gas valve is leaking or not? If you’re thinking about using an electronic gas detector, think again. This caused the replacement and return of many good valves.
The good news is there is a quick way to check for gas valve leakage using a CO measurement from the flue gas at equipment shutdown. If you’re already using CO testing to assure safe equipment operation, you can add this test to your bag of tricks.
As with any CO reading, you’ll need to get your measurements before dilution air is added to the flue gases. For natural draft equipment, you’ll need to test before the drafthood. When testing 80% or 90% equipment, measure a minimum of 12 inches past the induced draft blower outlet in the flue pipe. It’s best if you do this following NCI combustion safety testing protocols.
To test for valve leakage, watch the CO measurement for one minute after the burner shuts off. A properly operating system should have CO readings drop to zero ppm. This is a sign the valve is seated acceptably with no excessive fuel passing through. If CO readings spike within one minute of the burner shutting off, it can show a leaking gas valve.
The spike in CO shows raw fuel is leaking past the valve seats and contacting the hot metal surfaces of the heat exchanger. As the fuel makes contact, it converts to CO. This shows up on the combustion analyzer display as rising CO readings. They could appear as follows after the burner shuts down:
60 seconds | 50 seconds | 40 seconds | 30 seconds | 20 seconds | 10 seconds |
30 ppm | 20 ppm | 10 ppm | 40 ppm | 50 ppm | 60 ppm |
Readings like these require additional investigation to assure the gas valve is safe to leave in operation. If found to be unsafe, replace it. Don’t forget to check the gas piping too. If you don’t see a properly installed sediment trap, you need to install one. Otherwise, the issue could repeat in the future.
About the Author
David Richardson serves the HVAC industry as a curriculum developer and trainer at the National Comfort Institute, Inc. (NCI). NCI specializes in training focused on improving, measuring, and verifying HVAC and Building Performance.
If you’re an HVAC contractor or technician interested in learning more about adding carbon monoxide testing to your services, contact David at davidr@ncihvac.com or call him at 800-633-7058. NCI’s website www.nationalcomfortinstitute.com is full of free technical articles and downloads to help you improve your professionalism and strengthen your company.