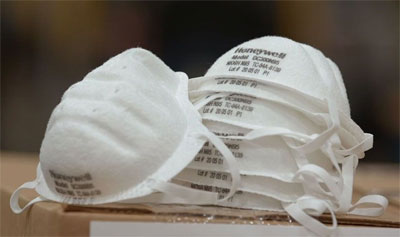
News
From WWII to Today: How a Building Was Transformed to Help with the Fight Against COVID-19
This site in Arizona was set up to produce N95 face masks to help during the coronavirus pandemic.
To help with the fight against coronavirus, a Honeywell facility in Phoenix has been repurposed to manufacture N95 face masks.
The campus it’s on was built in 1942 and was originally used for designing and producing engines for World War II. It has recently been used as storage for aerospace parts.
Now it’s also being used to produce masks to supply the Strategic National Stockpile for health care, safety and emergency services workers.
“There’s different ways to be heroes and this is one of them,” said Glen Tran, plant director who has led the transformation of the facility. “It’s an essential service that we’re doing.”
Speed and flexibility helped get the facility ready. “It took a lot of team effort from many different functions,” Glen said. And he knows first-hand about how to be flexible.
Here’s what it took to transform the facility.
1. Empty out the space
To get the facility ready, the inventory had to be removed. The Phoenix Engines facility has been dedicated to the design and manufacturing of aircraft propulsion engines and auxiliary power units (APU) since 1950. The specific building that has transformed to a mask-manufacturing site previously stored aerospace inventory like turbines. That had to go. The products were moved to a nearby facility.
2. Reconfigure everything
Next, the space had to be reconfigured. That included improving the lighting, redoing some of the flooring and bringing in new equipment. For example, printing machines to print the masks and ultrasonic welders to weld the bands to the masks.
3. Hire workers
With 500 roles to fill – there was a lot to get done. Two weeks ago, Glen was tapped to lead the effort to make masks in Phoenix. He abruptly moved from Seattle to Phoenix.
“We all had to play our part in accelerating this,” Glen said.
During his initial time in Phoenix, he was quarantined in a hotel room while handling logistics to get the site prepared to make masks. That included virtually hiring workers who will help make the masks.
4. Start production
It took a lot of people acting with urgency to get the site up and running in a short period of time, Glen said.
“To flip the switch, we had to ensure the people were properly trained, the equipment was all ready and the supply chain was readily available,” he said.
We shipped our first pallet of N95 masks on May 1— two weeks ahead of schedule.
Learn more about how Honeywell is helping respond to the coronavirus pandemic, including making more N95 masks in Rhode Island and making hand sanitizer in Michigan and Germany.