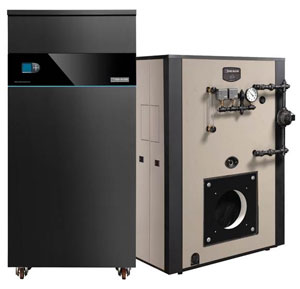
Products
Going Hybrid for Maximum Heating Efficiencies
By John Miller, Senior Product Manager, Weil-McLain
Two types of boilers can be better than one – especially when trying to minimize operating costs over the course of a heating season. By combining a large mass, non-condensing boiler with a high efficiency-condensing boiler – or “hybrid system,” you will ensure that your heating system is running at optimum efficiency.
Non-condensing boilers are designed to run at higher return water temperatures above 130 degrees to maximize longevity. The average efficiencies of non-condensing boilers range from 80-85 percent thermal efficiency. High temperature applications typically occur over the core heating season months of December through February.
Condensing boilers reach their maximum efficiency (upwards of 95 percent) when the return water temperature is below dew point and are more aligned with the milder heating season shoulder months of October, November, March and April. Running condensing boilers in high return temperature applications reduces their operating efficiency to marginally higher than non-condensing boiler designs.
By combining non-condensing and condensing boilers in a hybrid system boiler plant, users can reset building set points, reduce fuel consumption to lower operating costs and create comfortable, consistent building temperatures.
So why not just use an all high efficiency boiler plant? Consider the following benefits of a hybrid boiler system:
- Boiler Replacement Applications: Installing a hybrid system makes sense in existing, non-condensing replacement boiler applications. Most often, there are at least two high mass, non-condensing boilers in older boiler plants. Installing a high efficiency, condensing boiler in place of one of the failing high mass boilers now enables the efficiency benefits of the hybrid system. Further, this approach enables an incremental step in financing the overall boiler replacement capital outlay over time.
- New Build Applications: In short, condensing boilers cost more – upwards of 30-40 percent more than non-condensing boiler systems because of the non-corrosive heat exchanger materials required. Installing a hybrid system is more cost effective to purchase upfront and often achieves the greater portion of the energy savings of replacing an entire boiler plant with high-efficiency condensing boilers.
- Product Life / Longevity: Inherent to their design, non-condensing boilers have a longer product life, up to two times that of condensing boiler designs because of their thicker cast iron design and wider water pathways. Installing a hybrid system ensures a longer life of the boiler plant dedicated to the coldest heating season months.
Consider this example. A hybrid system could be utilized in an elementary school with two large cast iron boilers – one of which needs to be replaced after many years of dependable operation. The cast iron boiler is replaced with a Weil-McLain Evergreen™, SlimFit™ or new SVF™ high efficiency condensing boiler to match the heating requirement. The advanced Weil-McLain Unity™ control allows the assignment of an alternating, lead/lag boiler plant utilizing the new condensing boiler as the primary boiler over the heating season shoulder months and the existing non-condensing boiler for colder days.
Combining a durable Weil-McLain cast iron boiler with a high efficiency Evergreen, SlimFit or SVF condensing boiler can reduce wasted energy, lower utility costs and protect the environment with a smaller carbon footprint, while extending the life of the existing heating system at a lower acquisition cost.
The use of hybrid systems is becoming more and more common with engineers and building owners evaluating the heating efficiencies and other benefits of “going hybrid” in their current and new build heating systems. More frequently, commercial buildings such as medical facilities, apartment complexes, churches, schools, colleges, nursing homes and corporate campuses are standardizing on hybrid system boiler designs.
About the Author
John Miller is the commercial boiler senior product manager with Weil-McLain, a leading North American designer and manufacturer of hydronic comfort heating systems for residential, commercial and institutional buildings. Founded in 1881, Weil-McLain is based in the Chicago suburb of Burr Ridge, Ill., with manufacturing facilities in Michigan City, Ind. and Eden, N.C., and regional sales offices throughout the United States.