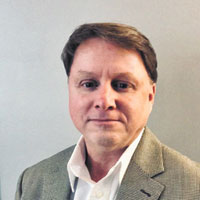
News
Inverter Driven – What Is An Inverter Driven System?
An inverter driven system (with respect to HVAC, because there are many others) is any mechanically compressed system controlled digitally with DC voltage, such that a variable speed compressor is produced, allowing system pressure change to occur at the compressor, not at the evaporator. Such pressure variation in the system at the compressor allows not only for more precise control at the evaporator (read that as a colder evaporator than in fixed speed systems) but to do so more energy efficiently than with fixed speed systems.
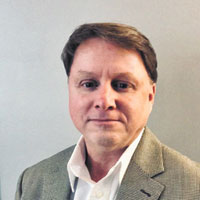
Traditionally with a fixed speed compressor and fixed metering device, as the evaporator loads with additional heat (return air temperature, humidity or airflow increases) the evaporating pressure will increase with additional load. On higher efficiency systems a TEV, or thermostatic expansion valve is used to vary the refrigerant flow to the evaporator. As the evaporator load increases, the TEV responds by opening and allowing more refrigerant to flow, hence maintaining pressure (more or less) at the evaporator. Now the system pressure variation takes place at the TEV, though practically speaking most TEVs have a “range” of about 1-ton beyond the nameplate rating (the bigger ones have a larger range; the smaller ones have less) above which they cannot flow more refrigerant, and below which they cannot accurately control (too low of a pressure drop across the TEV).
Though the refrigerant is better controlled by the variable metering device (TEV) than with a fixed metering device (such as a piston, variator, accurator, etc) the system as a whole is yet relegated to a fixed capacity due to a fixed speed compressor. The typical air conditioning system has a contactor controlled by 24v. circuit through the thermostat. On a call for cooling, the 24v. circuit is closed, energizing a coil in the outdoor unit contactor, the contact closes, the line voltage circuit is made to the compressor which comes on, full speed, at one fixed speed where it remains until the call is satisfied and the control circuit broken.
The inverter-driven system, though having the same goal as the fixed-speed system (i.e.: removal of heat, both latent and sensible) does so much differently, much more efficiently, more quietly and with much better performance (colder evaporator, greater latent heat removal) than the fixed speed system it replaces. The inverter system does not have a contactor, but instead converts 240v. AC to 340VDC (incoming voltage x 1.414 = DC voltage). That voltage is then “inverted”, or reformed back into a 3-phase sine wave that can be sent in very small increments called “hertz” (one cycle per second = one rps, or revolution per second of compressor crankshaft speed). As this now digital signal is fed to the compressor, one hertz at a time, the compressor can ramp up or down as needed.
The converter/inverter system begins at the circuit board with a variable voltage output, but not just to a variable speed compressor, but also to an EEV, the metering device with replaces the TEV. The electronic expansion valve is not unlike a stepper motor, powered by DC voltage. As such it can have a much greater range of operation than the TEV, allowing not only for more precise control at lower capacities, but in conjunction with a variable speed compressor, can provide a much greater refrigerant flow when higher capacities are needed (such as in heat pump applications).
Yes, the Inverter System involves an IPM and electronics (we’ll go deeper into the IPM, PCB, fault codes, ECM motors and more later), but it works in unison with a digital compressor to provide a soft start-up, quiet operation and it uses only the energy it needs (unlike a fixed speed, fully on or fully off motor/compressor). More importantly though, because the compressor is variable speed, and because the EEV is electronically modulated and can operate over a broad range of capacity, the system becomes, in fact, a variable refrigerant flow system and that variable flow can be controlled to make the indoor coil very cold. Much colder than a typical fixed speed system and certainly much more able to remove latent heat. The inverter driven system is just that: a system of inverter, compressor and EEV working in unison to provide the new wave in direct expansion heating and cooling.
Dan Applegate is a DFS/VRF National Trainer and a Senior Product Specialist.