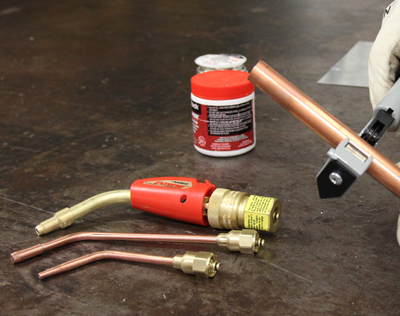
Tools
The Best Tool for Brazing and Soldering?
By Paul Eckoff, Director, Product Line Management, Alternative Market Channels, ESAB
The right tool for brazing or soldering pipe can be an air-fuel or oxy-fuel torch. The best choice depends on the type and diameter of the pipe, its location and considerations related to cost, safety, convenience and ease of use.
In actual practice for copper systems, most soldering occurs at temperatures of 350 to 550o F, while most brazing occurs at 1100 to 1500o F (depending on the temperature requirements of the flux and filler).
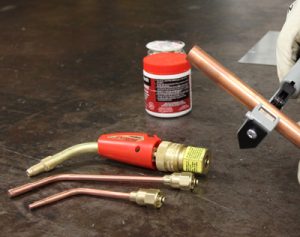
Target Heat
Target heat is the effective heat in a torch flame that can be applied directly to the target (as opposed to the actual heat of the flame, which is hotter). Common target heat temperatures include: 1750o F for air-swirl technology (air-propane), 2700o F for air-acetylene and 4700o F for oxy-acetylene.
Remember the goal is to heat the tube and fitting to a temperature high enough to melt the filler yet remain below the melting point of the base material. Further, capillary attraction must uniformly distribute the filler material between the pipe and fitting, so this means evenly distributing the heat on all sides of the target area.
Oxy-Acetylene
An oxy-acetylene torch with a welding tip concentrates the heat in a comparatively small area, while an oxy-acetylene torch with a multi-flame heating tip (rosebud) applies heat to a larger area. Due to the high temperatures, technicians need to continuously move the torch around the diameter of the pipe to evenly distribute the heat on all sides, as well as to prevent burn through.
In this category, the compact Victor® J-28 handle offers the flexibility to connect a welding tip, rosebud or cutting attachment. Adding a portable tote kit organizes gas cylinders and tools in a single package with a comfortable carrying handle.
Air-Swirl Technology
When it comes to evenly heating a target area, the “wrap around effect” of the TurboTorch® air-swirl flame sets the HVAC/R industry standard. With this technology, the torch tip meters a precise amount of pressurized gas to the venturi, which pulls in the exact amount of air to create a perfect air/fuel ratio in the mixing chamber. The pressurized gas then flows through a precision-machined helical rotor, becomes evenly mixed and then ignited in the flametube. The helical rotor’s spiral design also swirls and concentrates the heated gas as it exits the flametube at high velocity.
- Air-swirl technology delivers a creates a flame up to 40% hotter than other air-fuel torch designs. Other benefits include:
- Completely burning the fuel inside the flametube and creating a stable, blow-out resistant flame.
- Automatic metering to create a neutral flame; there is no need to adjust gas flow rates for different tip sizes or for wind and temperature conditions.
- A flame that wraps around all sides of the target to promote better heat transfer.
- A higher velocity flames that transfers heat better and minimizes the cooling effect of the ambient air.
- Better heat transfer to the target to decrease labor time and fuel cost.
- Self-lighting torch tips eliminate the need for a striker.
In a head-to-head competition between two skilled technicians, results will be very close, so the choice between oxy-fuel or air-swirl technology often comes down to personal preference. That said, there are some factual differences.
Air-swirl technology requires a single tank, so it’s more convenient to transport.
The air-swirl flame provides more forgiveness in lower temperature applications, such as brazing aluminum where the base metal melts at a temperature only 130o F higher than the filler material.
Conversely, the higher heat of an oxy-acetylene flame can braze larger diameter pipe, weld and cut steel and work better on a cold and windy rooftop. Oxy-acetylene also works well when a joint needs to be brought to temperature as quickly as possible to prevent heat from propagating downstream and affecting other HVAC/R components, such as gaskets inside valves and electronics.
In most HVAC/R applications, technicians will find an air-swirl torch more convenient, plus it eliminates the safety concerns associated with acetylene cylinders. In situations where oxy-acetylene provides the better heating characteristics, choose it to get the job done faster.