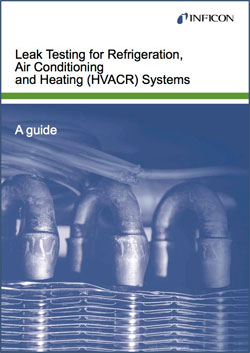
News
Checklist: 10 Avoidable Faults in Leak Testing of Refrigeration, Air Conditioning and Heating Systems
Inficon, one of the world’s leading manufacturers of instruments and devices for leak testing (www.inficon.com), has published a new e-book: “Leak testing of refrigeration, air conditioning and heating systems”. Checking these systems for leaks is a complex challenge. For example, even the (wrong) choice of leak test method, such as the water bath method, can cause the tester to overlook leaks because he has not considered the deformability and volume change of the test piece. Inficon has compiled a top 10 checklist of common leak testing errors that companies can avoid.
Error 1: The Wrong Method for the Test Leak Rate
A common error in the water bath method is that the tester does not detect bubbles even though there is a leak. Problematic: A basic condition for the suitability of a leak testing or leak detection method is the leak rate limit. Often, however, companies do not pay attention to this in practice. For example, they examine plastic parts using the pressure drop method without considering their deformability and the change in volume caused by the compressed air. The leak rates of the integral leak testing and subsequent leak detection must match.
Error 2: Incorrectly Selected Test Time in the Production Process
At what point in the production process does leak testing make sense? This should be carefully considered. It is usually helpful to check partial components before assembly. If the pre-assembled components fail the series test, the effort is significantly higher – and the time invested in assembly is lost.
Error 3: The Test Piece is Contaminated
The following applies to all test methods: Leak testing should always be carried out on completely new test parts. If a component was already in operation in advance and filled with oil or water, for example, small leaks may have clogged up. Before performing leak testing, test pieces must be cleaned and dried.
Error 4: Temperature Changes are Ignored
For integral leak testing according to the pressure decay principle or differential pressure measurement, temperature fluctuations are serious. Minimal temperature fluctuations can alter the measurable leak rate in several orders of magnitude.
Error 5: The Test Pressure Fluctuates
Companies should always fill the test piece with the same constant pressure during the leak testing. Caution is required, however, as the correct filling of some test pieces is only possible after a previous evacuation. With helium testing, for example, tracer gas concentrations are reduced in order to reduce testing costs.
Error 6: Stringer Leaks and Gross Leaks are Underestimated
Stringer leaks consist of capillary passages. For successful testing, it must be considered how long it takes for the tracer gas helium to be distributed in such a way that it also escapes from stringer leaks. Therefore, there should be sufficient time between filling and testing to be able to reliably identify stringer leaks.
Error 7: The Testers Do Not Know How to Perform Measuring
For integral leak testing it is recommended to use a reproducible measuring method instead of just relying on the tester’s perception. But one should consider how to measure and with which test medium. For example, air leak rates are specified, but helium has a slightly higher dynamic viscosity than air. Therefore, a conversion is required for the exact leak rate.
Error 8: No Calibration of the Test Equipment Takes Place
Companies should regularly check the operation and accuracy of their testing system with a reference leak (e.g. a calibration leak in a glass capillary), which always causes the same leak rate due to its defined size. If this leak rate is not determined in the testing, the test equipment has a malfunction.
Error 9: The Maintenance of the Test System is Neglected
If companies do not measure leak rates at a test station for days or for weeks that are higher than those at which the test piece still passes the test, this is either a sign of the immense quality of the product – or also an indicator of an insufficiently functioning test system. Therefore, companies should regularly check joints, hoses, test piece holders, etc.
Error 10: “We Can Do It Ourselves”
Think twice before making this decision. It is better to turn to experts and seek comprehensive advice. Selecting the best test method, configuring the test system properly and designing the test process as reliably as possible is a big challenge – therefore professional support is recommended.
The top 10 most common errors in leak testing are an excerpt from Inficon’s free e-book “Leak testing of refrigeration, air conditioning and heating systems – A guide”, which can be downloaded at https://www.inficon.com/markets/refrigeration/e-book/.
About INFICON
INFICON GmbH in Cologne, Germany, is one of the world’s leading developers, producers and suppliers of instruments and devices for leak testing. The leak detectors are used in demanding industrial processes in production and quality control and cover a wide range of applications. INFICON’s main customers are manufacturers and service companies of air conditioning and refrigeration equipment, the automotive and automotive supplier industry, the semiconductor industry and manufacturers of leak detection systems. Almost all manufacturers of cooling and air-conditioning equipment and their suppliers are customers. INFICON technology is used to test refrigerators, air conditioning systems and their components, heat pumps, drinking water dispensers, hot water storage tanks or gas boilers for the generation of hot water or for heating.
Embedded in the INFICON holding company based in Switzerland, the company uses key in-house components for its instruments, such as mass spectrometers and vacuum gauges. In 2006 INFICON revolutionized leak detection technology with tracer gas with the patented INFICON Wise TechnologyTM. In 2011, INFICON acquired Pfeiffer-Vacuum’s hydrogen leak detection business (the former Sensistor business unit).
INFICON can now look back on more than 50 years of experience in leak detection technology. Through production facilities in Cologne (Germany), Balzers (Liechtenstein), Linköping (Sweden), Syracuse (USA) and Shanghai (China) as well as through sales offices in all important industrial countries and an expanded network of sales partners, INFICON handles worldwide sales. In fiscal year 2016, INFICON AG with its approx. 950 employees achieved worldwide sales of US$ 310 million. INFICON’s registered shares (IFCN) are traded on the SIX Swiss Exchange.