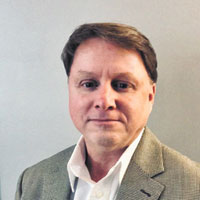
News
Inverter Driven: DFS is VRF
By Dan Applegate
Duct-free systems, mini-splits…all now are using inverter drive technology: Electronic Expansion Valves (EEV), driven by computer chips (EEPROM) which also control a variable compressor speed, based on information collected at various touch points throughout the system by thermistors. Thermistors (variable resistance/temperature) measure temperatures at the condenser outlet, compressor discharge and evaporator.
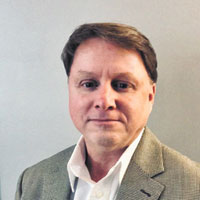
The temperatures are recorded as a partial voltage of the 5vdc returned to the PCB through the thermistor. The algorithms written on the computer chip determine how far to open the EEV, how fast and to what degree the compressor speed will be increased to accommodate the lower pressure drop. This is a variable refrigerant flow system.
There are of course, distinctions made between “duct free” equipment used primarily in residences (single phase electric) and “VRF” equipment which is primarily used in commercial applications (three-phase electric). DFS, or duct-free residential systems typically:
- Are powered by single-phase electric.
- Have indoor units that are powered and controlled from the outdoor unit.
- Have EEVs for all indoor units, in the outdoor unit.
- Are limited on largest multi-zone systems to eight or nine indoor units.
Whereas the VRF, or variable refrigerant flow commercial systems typically:
- Are powered by three-phase electric.
- Have indoor units powered from the main panel and use different control wiring (18-2 or wireless) than the DFS products.
- Have individual EEVS at each indoor unit.
- Have much greater diversity in type of product (heat recovery) and quantity of indoor units per outdoor unit chassis.
Regardless the application or product description, if the EEV responds to a computer command to precisely alter/control the refrigerant flow and the compressor is correspondingly sped up or down to match that change in pressure drop, then the system is in fact a variable refrigerant flow system, whether it is called DFS or VRF, or whether it is applied in a residential or commercial application.
Simply said, any inverter-driven technology will necessarily be controlled by computer. No longer are pressures in the system relevant as the EEV is driven by magnetic coils energized with pulsed dc voltage, and no longer is the compressor a fixed speed. Because that is true, inverter-driven equipment can experience conditions/faults/failures that may not otherwise be seen in a fixed refrigerant velocity/single-speed compressor system.
Consider this condition: the system is reporting a fault code for an IPM fault, compressor position error, or compressor current overdraw. Any one of these conditions could be caused by the very same thing on a variable refrigerant flow system that would not have occurred on a fixed speed system.
The soft ACR that is commonly used in DFS installations can be easily mis-handled. Leaks at the flare connection are the most common result, but lesser realized are the restrictions created in the tubing when bends are formed. When a lineset becomes deformed and a restriction is created, evaporator capacity is lost (due to increased pressure drop). The computer then cycles the compressor to a higher speed to increase refrigerant flow, something that couldn’t happen in a fixed speed, induction motor compressor system.
As a result of that inverter compressor’s increased speed (compensating for the increased system pressure drop through the liquid line) and depending on the degree of restriction, the suction pressure will drop disproportionately with discharge pressure, increasing compression ratio. As the compression ratio increases, so too does the discharge temperature and pressure leading to fault codes and possibly compressor failure.
A good example of this consequent condition found only in variable refrigerant flow systems, when a liquid line is to some degree compromised by improper handling/bending, occurs only in heating season. Given, the system installed this past cooling season was running great, customer pleased, only to have an unhappy customer when the weather turned chilly. Seems the homeowner, soon after setting the control to heat reported a very loud vibration coming from the indoor unit that certainly wasn’t there before. After numerous attempts to isolate the lineset and isolate the outdoor unit the vibration source still can’t be found.
It’s very likely the lineset, liquid line in particular, was not kept fully round during installation. Not sufficiently restrictive to affect cooling, the problem went unnoticed until heating season when, in need of greater refrigerant capacity, the compressor speed was increased. Increased refrigerant velocity induced vibration in the system not noticed in cooling, but very apparent in heating mode that could not be rectified any other way than than to replace the restricted lineset with one that was not restricted.
Variable EEVs and compressor speeds mean different considerations for DFS systems.
Dan (Applegate HVAC Consultants) is an independent trainer/instructor of inverter-driven technologies (DFS/VRF) to the HVAC industry. He can be reached at dan@vrftrainer.com.