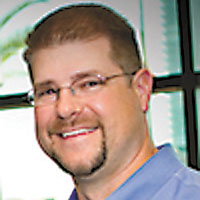
News
Carbon Monoxide: What Do You Know? Duct Connections that Kill Airflow and Heat Exchangers
In the middle of the summer heat, you probably aren’t thinking much about cracked heat exchangers. However, airflow is essential year-round in our industry. If you encounter systems with low cooling airflow, chances are high you also have messed up heating airflow.
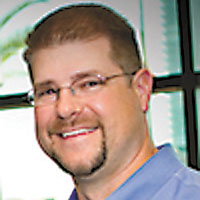
Low airflow through a furnace forces it to operate outside of manufacturer specifications. The heat exchanger overheats and may lead to premature equipment failure. Let’s look at some issues that may kill airflow and damage your customer’s systems.
Restrictive Return Fittings
Undersized return drops and sharp transitions restrict airflow and shorten equipment life. One solution to this problem is to add a return air inlet to the equipment when the capacity exceeds 80,000 Btu. Many will add a second return drop to the opposite side of the equipment or into the bottom of upflow equipment.
Contractors often assume a blower will pull airflow regardless of how they install the return fittings. If the duct is large enough to move the proper amount of air, it should work as intended.
However, this is a dangerous assumption to make. Depending on the number of turns built into fittings, severe airflow reduction can occur.
Sharp turns in a duct system effectively reduce the size of an opening when air attempts a 90-degree turn. As air tries to go around a sharp turn, it creates a tremendous amount of turbulence, and the air velocity decreases.
Make sure you correctly size and install your return fittings for the application. They work best when you use long sweeping bends that allow airflow a smooth path to travel back to the furnace.
Restrictive Air Filters
Installing the filter at the inlet of a furnace is another issue to consider. A filter installed in a poor location reduces its effectiveness because the entire filter area isn’t used. Factory filter racks are often undersized and allow unfiltered air to bypass the filter because of their design.
Incorrectly sized and restrictive filters also reduce airflow across the heat exchanger and lead to unnecessary overheating. Filters suffering from this problem create issues even when clean. They are too restrictive for the right amount of airflow that must move through them.
Consider increasing your filter sizes or add an extra filter when this is a concern. Adding a second return drop as described above allows space to add a second filter into the system. Using filter grilles is a simple way to increase filter surface area where conditions permit. Think twice about installing 100,000 Btu input furnaces with a single 16 x 25 x 1 filter.
Restrictive Coil
Installing an undersized coil on a larger furnace is expected in the north, where cooling loads are low, and heating loads are high. Typically, a tiny evaporator coil, matching the cooling load, sits on a huge furnace.
The smaller evaporator coil restricts airflow, causes a high pressure drop, and results in excessive supply static pressure. This installation kills heat exchangers, as the fan can’t move proper airflow through the coil. The furnace continually cycles on high limit causing undue heat exchanger stress and eventual failure.
Correct this condition by using a larger evaporator coil matching the size of the furnace, which will decrease static pressure and increase airflow.
Deadhead Plenums
Deadhead plenums or bullhead tees leave air with no direction as it exits a furnace. Air ends up “splatting” into the end of the duct, creating a tremendous amount of turbulent airflow.
Airflow performs best with at least three duct diameters out of the fan before it has to turn. If you ever experienced temperatures much warmer on one side of the duct system than the other, you see the results of this installation technique.
A better option is to use a properly sized plenum with take-offs with an opening sized approximately 50 percent larger than the duct. The bigger inlet gives air coming out of the furnace a low-pressure path to merge smoothly into the duct system.
Coil Panning and a Round Duct Plenum
The practice of panning off the top of an evaporator coil and tapping a round duct directly into it has never made sense. The fitting chokes off the coil opening and creates an extreme amount of turbulence.
Correct this issue by installing an extended centerline square-to-round transition from the coil to the round duct size. Air will flow much smoother out of the furnace with this style of duct fitting.
Premature heat exchanger failure and poor performance increase when any of these common installation mistakes exist. Who is to blame when the heat exchanger fails under conditions like this? It probably isn’t the equipment manufacturer’s fault.
David Richardson serves the HVAC industry as a curriculum developer and trainer at the National Comfort Institute, Inc. (NCI). NCI specializes in training focused on improving, measuring, and verifying HVAC and Building Performance.
If you’re an HVAC contractor or technician interested in learning more about adding carbon monoxide testing to your services, contact David at davidr@ncihvac.com. NCI’s website www.nationalcomfortinstitute.com is full of free technical articles and downloads to help you improve your professionalism and strengthen your company.