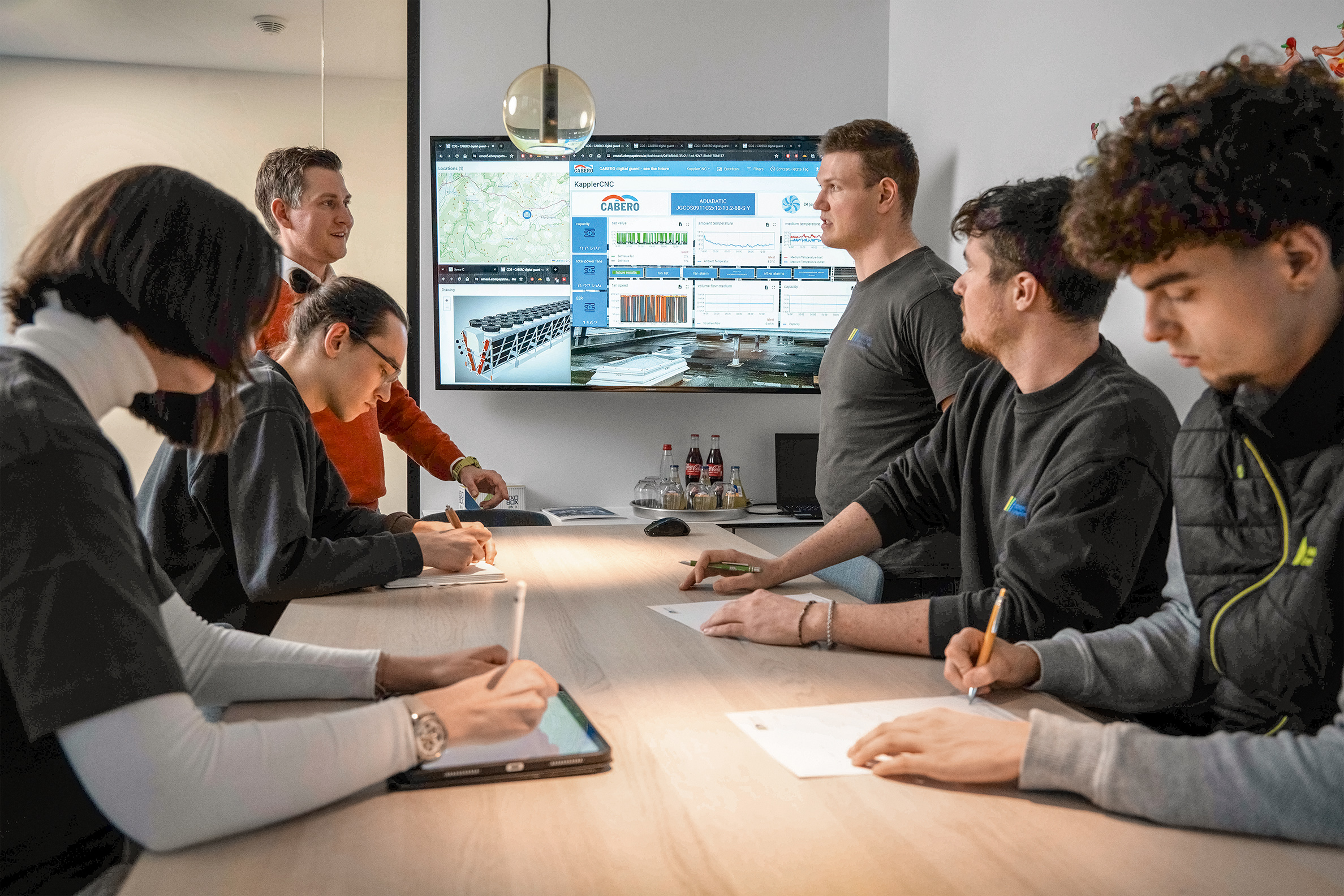
Manufacturers, Technology
Successful Project Shows Measurable Added Value with Digital Recooler
In a pioneering development project, Heidinger, Cabero and ebm-papst neo are demonstrating at Kappler CNC how system reliability and efficiency can be taken to a new level with the help of a digital twin.
ebm-papst neo, the Dortmund-based digital subsidiary of fan specialist ebm-papst, is using newly developed sensors to measure vibrations on the adiabatic recooler and analyze the air flow. The data from both measurements initially flows into an IntelliGate gateway, from where it is uploaded to the epCloud. Kappler GmbH & Co. KG, a leading international manufacturer of precision components based in Birkenfeld, was quick to embrace the project involving its recooler.
Precision in production and on the roof
Due to the sensitive precision components in production, temperatures at Kappler CNC are accurate to plus/minus one Kelvin throughout the entire production process. One system that contributes to this precise temperature control is the jumbo recooler system from Cabero installed by Heidinger in 2022 with 24 HyBlade axial fans with AxiTop diffusers from ebm-papst. The specialists from ebm-papst neo installed vibration meters and other sensors on all the fans. Data analysis enables conclusions to be drawn about the operating status by comparing the vibrations on the recooler with standard values. For Cabero, this provides important information on possible optimization potential in the design of the recoolers. For Heidinger, unexpected vibrations are a signal that a service call may be imminent and should be proactively scheduled.
Gateways and epCloud enable digital twin
The IntelliGate gateways are another component of the digitalization project. This is where all the data from the new sensors comes together and is uploaded to ebm-papst neo’s epCloud. Ultimately, the collection of data such as air flow, temperature, vibration and current draw makes it possible to create a model of the Kappler system: the so-called digital twin. This model can be used to determine the current status of the system and predict potential problems – which in turn enables Heidinger to react proactively to avoid unplanned downtime and service calls. The digital twin works completely independently and is decoupled from the Kappler network. Only authorized users can analyze the data and identify optimization potential for the customer.
At Kappler CNC, the digital twin has confirmed what everyone involved expected from its real-life counterpart: the system is running extremely efficiently and smoothly. Adrian Heidinger is enthusiastic about the project: “Projects like this show the real added value that intelligent technology can offer any company, even with little effort. Thanks to the minimal time and effort required for installation, we can also use targeted data analysis to determine where there are snags and where efficiency improvements are possible, even for companies with older systems.”
About ebm-papst
The ebm-papst Group, a family-run company headquartered in Mulfingen, Germany, is the world’s leading manufacturer of fans and motors. Since it was founded in 1963, the technological leader has set international industry standards with its core competencies in motor technology, electronics, digitalization, and aerodynamics. ebm-papst offers sustainable, intelligent, and tailor-made solutions for virtually every requirement in ventilation and heating technology.
In the 2022/23 financial year, the Group generated turnover of EUR 2.540 billion. It employs just under 15,000 people at 30 production sites (including in Germany, China, and the U.S.) and in 50 sales offices worldwide. ebm-papst sets the benchmark in almost all sectors, such as ventilation, air conditioning and refrigeration technology, heating technology, information technology, mechanical engineering, intralogistics, and medical technology.